

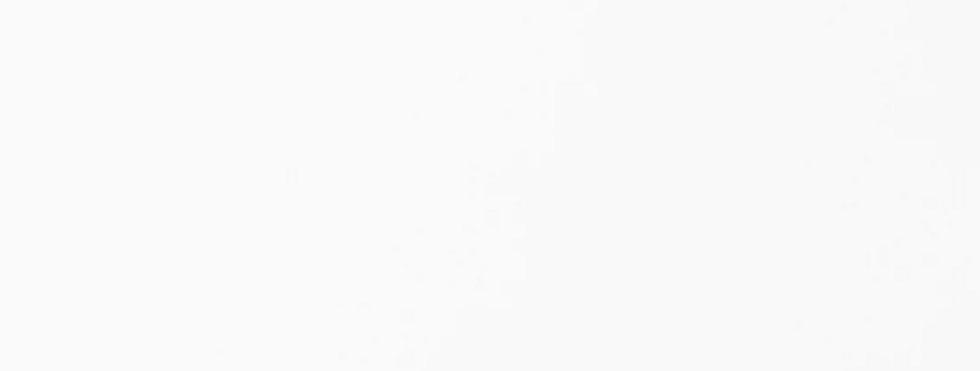
MOLTEN SALT STORAGE TANK DESIGN SERVICES

MOLTEN SALT STORAGE TANK DESIGN
Designing a molten salt storage tank involves several considerations to ensure safety, efficiency, and durability. Molten salt is often used as a thermal energy storage medium in concentrated solar power (CSP) plants, where it can store heat for long periods and release it as needed to generate electricity. Here are some key aspects to consider in the design:
-
Material Selection: The tank material must be able to withstand the high temperatures of molten salt, typically around 500-600°C (932-1112°F). Common materials include stainless steel, carbon steel, or specialized alloys like Inconel.
-
Insulation: Proper insulation is crucial to minimize heat loss and maintain the high temperature of the molten salt. Insulation materials such as ceramic fiber or refractory brick are commonly used to line the tank.
-
Sealing: The tank must be effectively sealed to prevent leakage of molten salt, which can be corrosive and pose safety hazards. Welded joints or specialized sealing techniques may be employed, depending on the tank material and design.
-
Thermal Expansion: Molten salt expands as it heats up, so the tank design must accommodate thermal expansion to prevent damage. Expansion joints or flexible connections may be incorporated into the design.
-
Heat Exchange System: Molten salt storage tanks are typically equipped with heat exchangers to transfer heat to and from the salt. These heat exchangers may consist of coils or tubes immersed in the molten salt, or external heat exchangers depending on the specific application.
-
Safety Features: Safety features such as pressure relief valves, temperature sensors, and overflow protection should be integrated into the design to prevent accidents and ensure safe operation.
-
Structural Integrity: The tank must be structurally robust to withstand the weight of the molten salt and any external loads. Structural analysis and engineering calculations are essential to ensure the tank's integrity under operating conditions.
-
Corrosion Resistance: Molten salt can be corrosive, particularly at high temperatures, so the tank material must be corrosion-resistant or protected with coatings or linings to prevent degradation over time.
-
Maintenance Access: Provision for maintenance and inspection access should be incorporated into the tank design to facilitate regular inspections, cleaning, and any necessary repairs.
-
Environmental Considerations: Environmental factors such as seismic loads, wind loads, and exposure to sunlight should be taken into account in the tank design to ensure long-term durability and stability.
Overall, designing a molten salt storage tank requires a comprehensive understanding of the thermal, mechanical, and chemical properties of molten salt, as well as sound engineering principles to ensure the safety and efficiency of the storage system. Collaboration between engineers, materials specialists, and safety experts is essential to develop a robust and reliable design.
MOLTEN SALT STORAGE TANK DESIGN, INSTRUMENTATION
Instrumentation plays a critical role in monitoring and controlling a molten salt storage tank system to ensure safe and efficient operation. Here are some key instruments commonly used in molten salt storage tank design:
-
Temperature Sensors: Temperature sensors are essential for monitoring the temperature of the molten salt within the tank. Thermocouples or resistance temperature detectors (RTDs) are commonly used for this purpose. Multiple sensors may be distributed throughout the tank to provide temperature profiles and ensure uniform heating and cooling.
-
Level Sensors: Level sensors are used to monitor the level of molten salt within the tank. Capacitance, ultrasonic, or radar level sensors can be used to provide accurate level measurements even in high-temperature environments. Maintaining proper salt level is crucial for efficient heat storage and retrieval.
-
Pressure Gauges: Pressure gauges are used to monitor the pressure inside the tank. This helps ensure that the tank remains within safe operating limits and can provide early warning of any potential issues such as overpressure conditions.
-
Flow Meters: Flow meters are used to measure the flow rate of molten salt during charging and discharging operations. This helps ensure accurate control of the thermal energy transfer process and can aid in optimizing system performance.
-
Safety Interlocks: Various safety interlocks may be implemented to ensure safe operation of the tank system. These interlocks may be triggered based on parameters such as temperature, pressure, or level, and can initiate emergency shutdown procedures if necessary.
-
Control Systems: Control systems play a crucial role in regulating the operation of the molten salt storage tank. Programmable logic controllers (PLCs) or distributed control systems (DCS) can be used to monitor sensor inputs, implement control algorithms, and actuate valves and other equipment as needed to maintain desired operating conditions.
-
Alarms and Indicators: Visual and audible alarms can alert operators to abnormal conditions such as high temperatures, low levels, or pressure excursions. These alarms can help operators respond promptly to potential issues and prevent accidents.
-
Data Logging and Monitoring: Data logging systems can record sensor measurements and system parameters over time for analysis and troubleshooting. Remote monitoring capabilities may also be incorporated to allow operators to monitor the tank system's status and performance from a central control room or via mobile devices.
-
Corrosion Monitoring: In addition to sensors directly related to the operation of the tank, instruments for monitoring corrosion rates or the condition of protective coatings may be employed to ensure long-term integrity and reliability of the tank system.
-
Calibration and Maintenance Tools: Regular calibration and maintenance of instrumentation are essential to ensure accurate and reliable operation. Proper calibration tools and procedures should be in place to verify the accuracy of sensors and instruments on a periodic basis.
By integrating these instrumentation and control systems into the molten salt storage tank design, operators can effectively monitor and manage the thermal energy storage process, optimize system performance, and ensure safe and reliable operation over the long term.
MOLTEN SALT STORAGE TANK DESIGN, SIZING
Designing the size of a molten salt storage tank involves several factors, including the specific requirements of the thermal energy storage system, the desired duration of energy storage, and the power output capacity of the associated power generation system (e.g., a concentrated solar power plant). Here's a step-by-step approach to sizing a molten salt storage tank:
-
Define System Requirements: Determine the thermal energy storage requirements of the system. This includes the maximum and minimum operating temperatures, the required storage capacity in terms of energy (kWh or MWh), and the desired duration of energy storage (e.g., hours of storage).
-
Calculate Energy Storage Capacity: Calculate the total energy storage capacity required based on the power output of the associated power generation system and the desired duration of energy storage. This can be calculated using the formula:
Total Energy Storage Capacity (MWh) = Power Output (MW) × Storage Duration (hours)
-
Select Molten Salt: Choose an appropriate molten salt composition based on its thermal properties, such as specific heat capacity and thermal conductivity, which affect the energy storage density and efficiency of the system.
-
Determine Salt Volume: Calculate the volume of molten salt required to store the total energy calculated in step 2. This can be calculated using the formula:
Salt Volume (m³) = Total Energy Storage Capacity (MWh) / Salt Density (kg/m³)
The salt density will depend on the specific composition of the molten salt chosen for the system.
-
Consider Tank Geometry: Determine the appropriate tank geometry based on factors such as available space, construction considerations, and cost constraints. Common tank shapes include cylindrical, spherical, or rectangular.
-
Factor in Heat Losses: Account for heat losses from the storage tank during charging and discharging cycles. Proper insulation and thermal modeling can help estimate these losses and ensure that the tank size is adequate to meet the required energy storage capacity.
-
Safety Margins: Include safety margins in the sizing calculations to account for variations in operating conditions, transient loads, and uncertainties in the system parameters.
-
Optimization: Iterate on the design to optimize the size of the storage tank while meeting the system requirements and considering factors such as cost-effectiveness and practicality.
-
Review and Validation: Review the sizing calculations with relevant stakeholders, including engineers, designers, and project managers, to validate the design and ensure that it meets the project objectives.
-
Detailed Design: Once the size of the storage tank is finalized, proceed with the detailed design, including structural analysis, material selection, and integration with the rest of the thermal energy storage system.
By following these steps, you can effectively size a molten salt storage tank to meet the specific requirements of your thermal energy storage system and ensure optimal performance
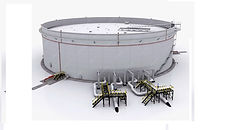



Wisdom is one of the leading design Service provider for oil & Gas, Petrochemical & process Industries