WISDOM ENGINEERING
mail: sravani@consultant.com

MUMBAI, , INDIA
Whatsup message or call 24/7 availible
Phone & Whatsup: +91-8374485833,
mail: sravani@consultant.com




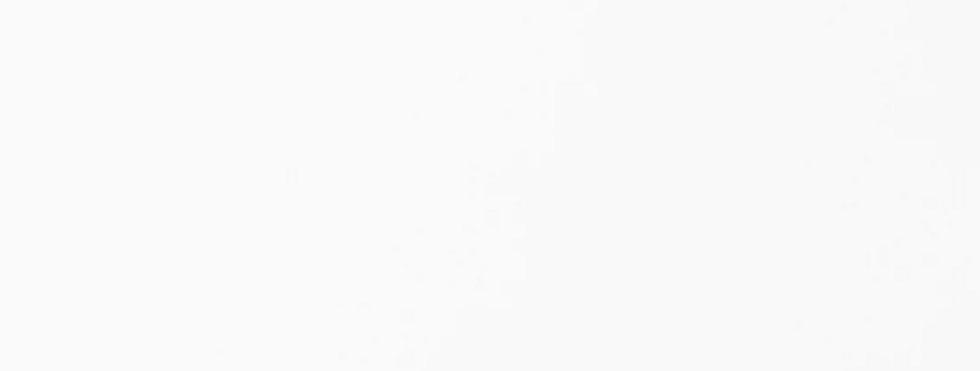
STEEL WATER STORAGE TANK DESIGN SERVICES

steel water storage tank design
Designing a steel water storage tank involves several considerations to ensure structural integrity, safety, and functionality. Here are the basic steps involved:
-
Determining Requirements: Understand the purpose of the tank, the volume of water it needs to store, and any specific requirements such as location, seismic conditions, or environmental regulations.
-
Selecting Material and Type: Choose steel as the material for the tank due to its durability and strength. Determine the type of tank based on factors like usage (potable water, industrial, agricultural), location (above ground, below ground), and shape (cylindrical, rectangular).
-
Calculating Dimensions: Calculate the necessary dimensions of the tank based on the required storage capacity, considering factors like height, diameter, and wall thickness.
-
Designing Foundation: Design a suitable foundation to support the weight of the tank and the stored water. Factors such as soil type, bearing capacity, and seismic conditions will influence the foundation design.
-
Structural Design: Develop the structural design of the tank, including the shell (side walls), roof, and base plate. Consider factors such as material properties, internal and external loads, wind and seismic forces, and corrosion protection.
-
Tank Accessories: Include necessary accessories such as inlet and outlet pipes, overflow pipes, vents, manholes, and access ladders or platforms. Ensure proper placement and sizing of these components for efficient operation and maintenance.
-
Coating and Linings: Apply appropriate coatings or linings to protect the steel from corrosion and extend the tank's lifespan. Consider factors such as water quality, temperature, and chemical exposure when selecting coatings.
-
Seismic and Wind Load Analysis: Conduct analysis to ensure the tank can withstand seismic events and wind loads according to applicable building codes and standards.
-
Quality Control and Inspection: Implement quality control measures throughout the fabrication and construction process to ensure compliance with design specifications and safety standards.
-
Maintenance Considerations: Develop a maintenance plan to monitor the condition of the tank, inspect for corrosion or damage, and perform necessary repairs or maintenance activities to ensure continued functionality and longevity.
Throughout the design process, it's essential to consult relevant codes, standards, and regulations, such as AWWA (American Water Works Association) standards, API (American Petroleum Institute) standards, and local building codes, to ensure compliance and safety. Additionally, involving experienced engineers and professionals in the design and construction process can help ensure a successful outcome.
You
instrumentation
Instrumentation for a water storage tank typically involves monitoring and controlling various parameters to ensure efficient operation, safety, and regulatory compliance. Here are some common instruments used:
-
Level Measurement:
-
Ultrasonic level sensors: These sensors use sound waves to measure the distance from the sensor to the water surface.
-
Radar level transmitters: They utilize radar waves to determine the distance to the water surface, providing accurate level measurements even in harsh environmental conditions.
-
Float switches: Simple devices that activate or deactivate based on the water level, often used for high and low-level alarms.
-
-
Pressure Measurement:
-
Pressure transmitters: These instruments measure the pressure exerted by the water inside the tank, helping to monitor the tank's integrity and water flow.
-
Pressure gauges: Visual indicators displaying the pressure inside the tank.
-
-
Temperature Measurement:
-
Temperature sensors: These devices measure the temperature of the water, helping to monitor and control temperature-sensitive processes or prevent freezing in cold climates.
-
-
Flow Measurement:
-
Flow meters: Instruments used to measure the flow rate of water entering or leaving the tank, providing important data for water usage monitoring and process control.
-
-
Water Quality Monitoring:
-
pH meters: Measure the acidity or alkalinity of the water.
-
Conductivity meters: Measure the ability of the water to conduct electricity, indicating its purity.
-
Dissolved oxygen meters: Measure the amount of oxygen dissolved in the water, important for aquatic life and water treatment processes.
-
-
Control Systems:
-
Programmable Logic Controllers (PLCs) or Distributed Control Systems (DCS): These systems automate control processes based on input from various sensors, allowing for remote monitoring and control of the tank's operations.
-
Supervisory Control and Data Acquisition (SCADA) systems: Monitor, gather, and process real-time data from multiple sensors and control devices, providing operators with a comprehensive view of the tank's status and allowing for remote control and troubleshooting.
-
-
Alarm Systems:
-
High and low-level alarms: Alert operators when the water level in the tank exceeds predefined thresholds, indicating potential overflows or shortages.
-
Pressure and temperature alarms: Notify operators of abnormal pressure or temperature conditions inside the tank, signaling potential issues with the tank or the water quality.
-
Proper instrumentation and control systems help optimize the performance of water storage tanks, ensure compliance with regulations, and enhance safety and efficiency in water management processes.
You
welding
Welding plays a crucial role in the fabrication and construction of steel water storage tanks. Here's an overview of welding processes commonly used in tank fabrication:
-
Shielded Metal Arc Welding (SMAW):
-
Also known as stick welding, SMAW is a manual welding process that uses a consumable electrode coated in flux.
-
It's versatile and can be used in various positions, making it suitable for welding tank components such as shell plates, roof plates, and structural supports.
-
-
Gas Metal Arc Welding (GMAW):
-
Commonly referred to as MIG (Metal Inert Gas) welding, GMAW uses a continuous solid wire electrode and a shielding gas, typically argon or a mixture of argon and carbon dioxide.
-
It's suitable for welding thin to thick materials and is often used for welding circumferential seams in tank shells and attaching nozzles and fittings.
-
-
Flux-Cored Arc Welding (FCAW):
-
Similar to GMAW, FCAW uses a continuous wire electrode, but it has a flux core that provides shielding, eliminating the need for an external shielding gas.
-
FCAW is often used in outdoor or windy conditions where gas shielding may be difficult to maintain. It's suitable for welding thicker materials and can be used in various positions.
-
-
Submerged Arc Welding (SAW):
-
SAW involves feeding a continuous wire electrode and a granular flux into the weld zone while the arc is submerged under a layer of flux.
-
It's a high-productivity welding process suitable for welding long seams in tank shells and other large structural components.
-
-
Gas Tungsten Arc Welding (GTAW):
-
Also known as TIG (Tungsten Inert Gas) welding, GTAW uses a non-consumable tungsten electrode and a shielding gas, typically argon.
-
GTAW produces high-quality, precise welds and is often used for welding critical components like nozzles, fittings, and small-diameter pipes.
-
-
Plasma Arc Welding (PAW):
-
PAW is similar to GTAW but uses a constricted plasma arc for higher energy density and increased welding speed.
-
It's suitable for welding thin materials and can produce welds with minimal heat input and distortion, making it useful for certain tank fabrication applications.
-
Proper welding procedures, including pre-weld preparation, joint design, welding parameters, and post-weld inspection, are essential to ensure the integrity and reliability of welded joints in water storage tanks. Welders should be qualified and certified according to applicable codes and standards, such as AWS (American Welding Society) D1.1 for structural welding or API (American Petroleum Institute) standards for tank fabrication. Additionally, proper welding techniques and safety practices must be followed to minimize defects and ensure the safety of personnel and the environment.
You
foundation
The foundation of a water storage tank is crucial for ensuring its stability, durability, and long-term performance. Here's an overview of the steps involved in designing the foundation for a steel water storage tank:
-
Site Investigation:
-
Conduct a thorough geotechnical investigation of the site to assess soil properties, bearing capacity, groundwater conditions, and potential environmental factors that may affect the foundation design.
-
-
Foundation Type Selection:
-
Choose an appropriate foundation type based on soil conditions, tank size, local building codes, and project requirements.
-
Common types of foundations for water storage tanks include:
-
Concrete Slab Foundation: Suitable for smaller tanks or tanks with uniform loading conditions.
-
Ringwall Foundation: Consists of a reinforced concrete ringwall around the perimeter of the tank base, providing support for the tank walls.
-
Spread Footing Foundation: Utilizes large concrete footings spread across the tank base to distribute loads to the underlying soil.
-
Pile Foundation: Driven or drilled piles are used to transfer loads to deeper, more stable soil layers, suitable for areas with weak or expansive soils.
-
-
-
Foundation Design:
-
Determine the dimensions and thickness of the foundation elements based on structural requirements, soil bearing capacity, and anticipated loads from the tank and its contents.
-
Consider factors such as dead loads (weight of the tank and its components), live loads (weight of water and any additional equipment), wind loads, seismic loads, and temperature effects.
-
Design the foundation to resist settlement, uplift, and lateral forces, ensuring stability and preventing overturning or sliding.
-
-
Reinforcement and Reinforcement Detailing:
-
Provide reinforcement, such as steel rebars or mesh, within the concrete foundation elements to enhance structural strength and durability.
-
Detail reinforcement placement, spacing, and anchorage to ensure proper load transfer and resistance to cracking and deformation.
-
-
Construction and Quality Control:
-
Follow approved construction drawings and specifications for foundation construction, ensuring proper placement, compaction, and curing of concrete.
-
Implement quality control measures, such as concrete testing, inspection of reinforcement, and monitoring of construction activities to ensure compliance with design requirements and standards.
-
-
Grading and Drainage:
-
Grade the area around the tank foundation to promote proper surface water drainage away from the tank and prevent ponding or erosion.
-
Install drainage features, such as swales, gutters, or French drains, to manage groundwater and surface water runoff effectively.
-
-
Final Inspection and Certification:
-
Conduct a final inspection of the completed foundation to verify compliance with design specifications, safety standards, and regulatory requirements.
-
Obtain any necessary certifications or approvals from relevant authorities before proceeding with tank installation.
-
Proper foundation design and construction are essential for the safe and reliable operation of water storage tanks. Engaging qualified geotechnical and structural engineers, adhering to industry best practices and standards, and conducting thorough quality control and inspection throughout the construction process are critical for ensuring the integrity and performance of the tank foundation.
You
itp
IPT can stand for various things depending on the context. One common meaning is "Inspection and Test Plan." An Inspection and Test Plan (ITP) is a document that outlines the sequence of activities, inspection points, and tests that need to be conducted during the construction or fabrication process to ensure compliance with project specifications, standards, and regulatory requirements.
An ITP typically includes the following components:
-
Scope: A brief description of the project or activity covered by the ITP.
-
References: Relevant codes, standards, specifications, drawings, and other documents to be followed during inspection and testing.
-
Responsibilities: Roles and responsibilities of project personnel, inspectors, and testing agencies involved in the execution of the ITP.
-
Inspection Points: Specific checkpoints or milestones in the construction process where inspections are required to verify compliance with requirements.
-
Testing Procedures: Detailed procedures for conducting various tests and measurements to assess the quality, performance, and functionality of materials, components, or systems.
-
Acceptance Criteria: Criteria or standards used to evaluate the results of inspections and tests and determine whether the work meets specified requirements.
-
Documentation Requirements: Documentation and record-keeping procedures for recording inspection and test results, including forms, reports, and certificates.
-
Non-Conformance Management: Procedures for addressing and resolving non-conformities, deviations, or deficiencies identified during inspections and testing.
-
Approval and Sign-off: Signatures of authorized personnel indicating approval and acceptance of completed inspections and tests.
An ITP serves as a roadmap for quality assurance and quality control activities throughout the project lifecycle, helping to ensure that construction or fabrication work is carried out according to established standards and specifications. It provides a systematic approach to verify that project requirements are met and that the final product meets the desired quality standards.

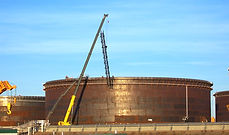

